Hello from Oakland,
First up, please accept our apologies for the tardiness of this month’s backer update. We welcomed our son Ira Aaron Vincent into the family on December 3 and the last few weeks have been happy, but somewhat sleep deprived. If this update is a bit shorter or less coherent than you’ve come to expect, this is the guy you can blame:
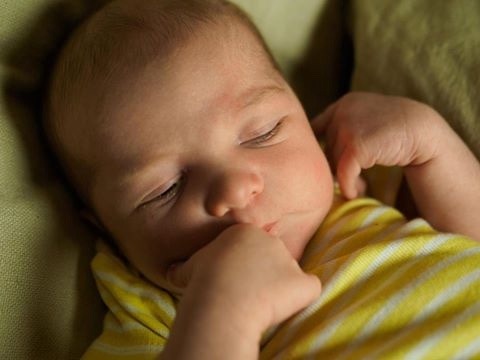
Ira Aaron Vincent was born December 3, 2016 at 10:10 PM
While we haven’t been getting a whole lot done in Oakland, our factory has been hard at work marshaling the resources for our PVT (production test) run and for mass production. This hasn’t gone as quickly as we’d have liked, but we’ve been making steady progress.
[[MORE]]Schedule
Last week, the factory sent us updated samples of the wooden enclosure, the baseplate, the center bars, the rails, the rubber feet, the screw for the stand, and the Type C cables. We’re eagerly awaiting the package, which DHL says should arrive on Tuesday. The final samples of the keycaps they were supposed to send came back from the painting shop and were judged to not be of good enough quality to send along. The factory has said we should expect them this weekend along with the final sample of the plastic stand.
Right now, the longest lead time components are the wooden enclosures, name-brand RJ45 jacks and name-brand LEDs. We’re starting to run up against Chinese New Year, when all manufacturing and commerce in China shuts down for about 3 weeks. Factories will start to close on or about January 15.
Our wood supplier has told us that if we place the production order within the next few days, they can promise 500-600 sets of keyboard enclosures before they close up shop for the holidays. As of now, this is the limiting factor on how many keyboards we expect to be able to produce in January. As soon as the “golden sample” arrives, we’ll check it to make sure they’ve fixed the problems in the last version and ask them to spin up the CNCs.
The factory thinks they’ll be able to ship the first 500 production units before Chinese New Year, but we’re pretty sure that’s not actually plausible. Once folks are back at work in early February, Jesse will be back in Shenzhen to do everything possible to push things forward.
A small gift for you
There’s no way we can express how much it’s meant to us that you all have been so supportive as we’ve worked our way through the design and manufacturing process, but we wanted to do _something_ to say “thank you”
When we launched the Kickstarter campaign, we told you that we’d be offering you a choice of keycap labels. Many of you have asked about the cost of additional sets of keycaps. I think we’ve previously said that we expect that extra keysets will cost about $40.
Every keyboard ordered before December 31, 2016 will come with a set of QWERTY keycaps preinstalled, as well as a second set of keycaps for free. As of now, it looks like you’ll be able to choose between (at least) QWERTY, Dvorak, Colemak, Runes and a blank variant.
We know that extra keycaps don’t in any way make up for how long it’s taken to get your Model 01’s made, but we hope that you’ll enjoy them.
A team of folks from the community has been hard at work on our non-QWERTY key layouts. We’re thrilled and amazed by what they’ve come up with so far.
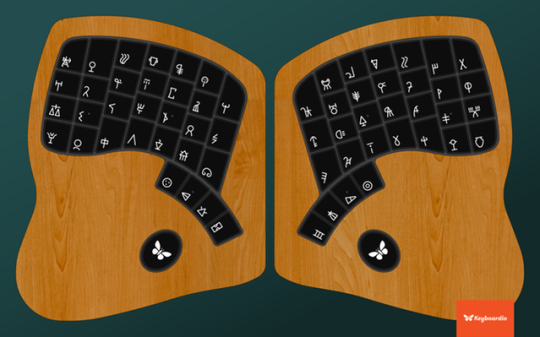
Michael Richters is primarily responsible for the Linear A “runic” layout. He has a few more changes to make before it’s set in stone.
Here’s the status of each part:
Wooden Enclosure
Over the past month, we’ve been working with our factory and the wood CNC factory to finalize the dimensions of the Model 01’s wooden enclosure. What we’d found on the previous samples was that while the wood was perfectly sized coming off of the CNC, it managed to shrink by a fraction of a millimeter before it was finished. As it turns out, this was just enough that plastic base plates were hard to fit into the wood, and, once installed, tended to push against the wood. In at least one case, this caused the wooden enclosure to crack.
Once we brought this to the CNC factory’s attention, they made a small change to the enclosure’s dimensions and milled a new set of samples. Our factory tested them over the course of a week, pronounced them to still fit well after sitting in the humid Shenzhen air and sent a set of samples onward to us on Tuesday. Once we verify that they _still_ fit well after their international flight and a few days in the unseasonably cold and dry California air, we’ll ask the factory to start cranking out the wooden enclosures for PVT.
They’ve guaranteed that they can finish the PVT enclosures within two weeks and said that they should be able to do another 500. We’ll see.
Base plates
After a fair bit of back and forth, the injection molding factory making the keyboard’s baseplates finally completed what was supposed to be the final modification of the tooling before PVT last Friday. This change removes the pockets for the old feet and adds extra internal “ribbing” to help the base plates stay rigid. It also slightly modifies the tooling to use a mixture of ABS and Polycarbonate, again to give the baseplates more strength.
Samples of the updated design are in a package on their way to us now. Our factory has told us, however, that they’re upset with the contract factory who’s doing this work and that the quality of the parts coming out of the updated tooling isn’t yet usable. They expect that the next version of the tooling will take another week and are meeting with the management team at the injection molding factory to try to press them to get their act together. Our factory says they’re planning to send their mechanical engineer to babysit the injection molding factory while they update the tooling.
Metal keyplates
The tooling for the metal keyplates has been done for quite a while now. Once we’re ready to make everything else, the metal stamping factory can churn thousands of them out in about a week.
Center bars
The tooling for the updated versions of the center bars that you can use to keep the two halves of your Model 01 together were finished about a week ago and samples are on their way to us now. There are still some issues with the bottom surface of those parts and the factory is working to make slight changes to the tooling to resolve them. These parts, at least, are being made in-house by our factory, so the turn-around time is expected to be quick.
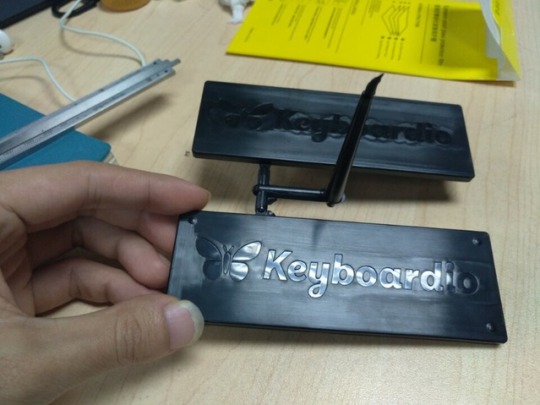
The surface treatment on the updated center bars isn’t quite up to snuff yet, but the factory is on it
Rails
The rails that hold the center bar to each half of the keyboard have been updated to include built-in brass nuts. The factory has sent us samples for final approval.
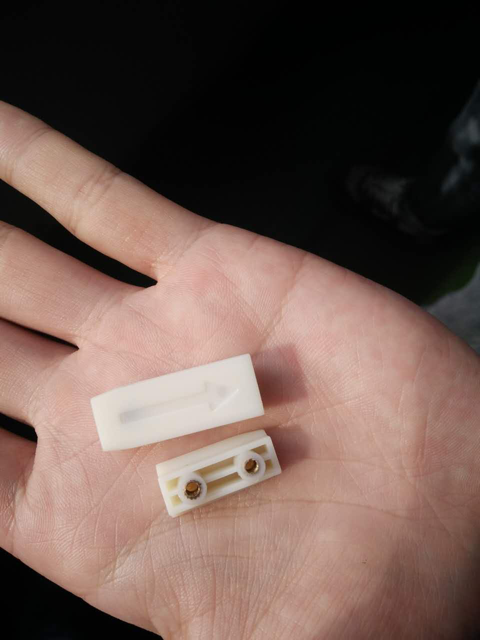
The production rails will be black, but these updated samples are the first to have embedded brass screws
Stands
Earlier this month, the factory sent us CNC-milled samples of the wooden and plastic versions of the new “starfish” stand. We found that the bottom side of the plastic stand had just a little bit too much give to it. The factory made a slight tweak to the design to fix this and had a new sample made. That sample should be done tomorrow. At the same time, they’ve put the stands out to bid at three injection molding factories and found one who are promising a 3 week leadtime for tooling.
The first version of the rubber feet that the factory put on the stands weren’t grippy enough, so they’re sending over a new version with a bit more texture to them.
This is still a little bit too long for PVT, so the folks who are doing our wooden enclosures put together a sample of a wooden version of the stand. It’s going to be fairly expensive to make, but we can do a small run of them with a very short lead time. The current plan is to use the wooden stands for the 100 PVT units and then to (hopefully) make them available for sale later.
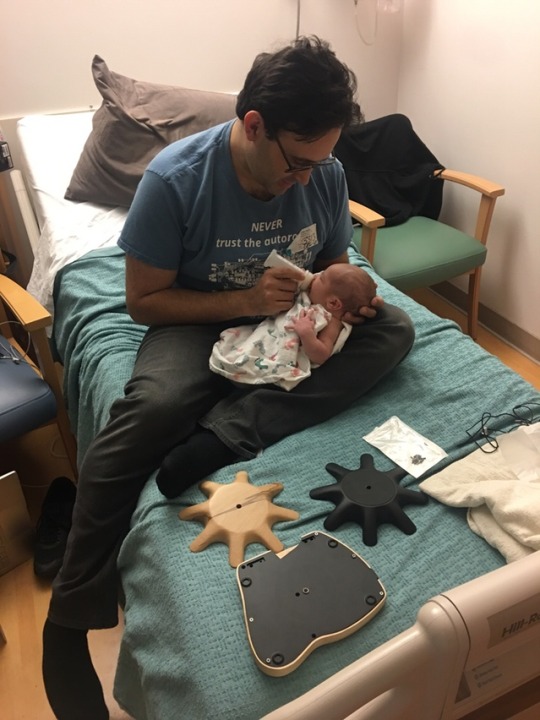
You can see samples of the wooden and plastic stands in the foreground of this photo
Keycaps
At this point, we think that the keycap molds are all set, though we’re still waiting on a report from the factory confirming how much force is required to insert and remove the keycaps. This will help us make sure that the keycaps are easy to assemble and easy to replace, but won’t fall out when you don’t want them to.
We’d expected a sample of the production version of the labeled QWERTY keycaps to show up this week, but when the factory got them back from the painting shop, they found that the quality of the painting wasn’t up to snuff. It turns out that the jigs they use to paint the keycaps need a small modification to let the paint cover the bottom edges of the keycaps. For the PVT run, the factory has developed a hack to work around this. At the same time, they’re modifying the jigs for mass production.
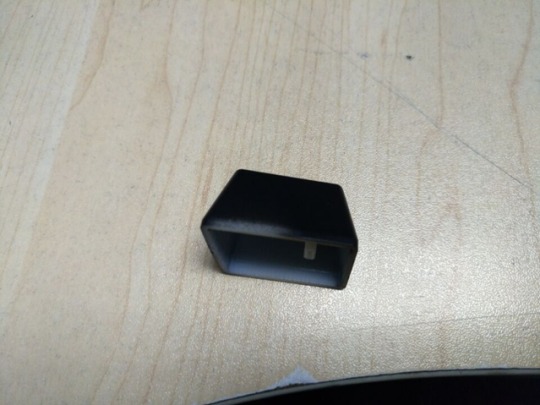
This photo from the factory shows the painting problem they’re working to rectify
Stand screws
The stands screw to the bottom of the keyboard with standard ¼-20" tripod screws. Our factory has had some trouble sourcing the right screws. Over the past few weeks, they’ve sent us samples that had screw threads that were just wrong enough to be a problem, as well as samples that were fairly cheaply made, with the handle just not very well attached to the screw. This week, they showed us photographs of a much nicer looking all-metal tripod screw. Samples of this new screw are winging their way to us now.
Packaging
The factory’s packaging supplier has sent them sample of a packaging design, but we’ve been told that it’s “way too big” and they’re taking another stab at it.
USB Cables
Earlier this month, the factory sent us samples of a proper 1.5M USB cable with a right-angle USB-C connector on the other end. We asked them to find us a second source so that we could compare the quality (and verify that one or both of them have the correct embedded resistor to meet the USB Type C spec).
The second sample should arrive on Saturday or Monday. After that, we can select one cable and the factory can place the order.
RJ45 Cables
The two halves of the Model 01 are connected by an RJ45 cable. We’ll be shipping your Model 01 with a short cable and a long cable. The factory showed us first samples of these four months ago. We’re expecting them to send the final samples for approval next week.
RJ45 Connectors
Each half of the Model 01 has an RJ45 jack to plug that cable into. Originally, we were using a Taiwanese jack, but our factory told us that the lead times were just too long and recommended a locally made version to try instead. Well, we tried it. And this month, one of those jacks cracked in a way we didn’t like after far less abuse than it should have taken, so we told the factory they needed to switch back to the part we’d originally specified. They sent samples of the newly-sourced original part for us to verify. After that, we’ll make a tiny change to the circuit board design so the new/old jack fits correctly and then crank out the PCBs for PVT.
LEDs
We’ve been continuing to track the acoustic noise problem with the LEDs that we’ve mentioned in previous backer updates. You might remember that we’d found a partial solution that involved swapping out some inductors and capacitors. We worked on tuning that solution and while it managed to cut down the noise, it wasn’t perfect and came at the cost of some components that would be more prone to failure.
We’d been pretty sure the problem was a PCB layout issue, but it turned out to have been caused by the specific LEDs the factory had sourced for the Model 01. Because the APA102C LEDs we’d originally specced had a long lead time, the factory had found a few locally made alternative LEDs that were supposed to be 100% compatible. As it happens, they’re compatible, just not exactly the same. And in our use case, they whine.
We reached out to APA, the original manufacturer to see what they could do for us. They were able to ship enough LEDs for the PVT run immediately, but have told us that we’re looking at a 12+ week lead time for volume delivery of APA102C LEDs. They offered us two other new options, the 102-2C and the 102-22C. We got the 102-2C LEDs. After discovering that they also had the noise problem, we took a look at the chip inside them and discovered that they appear to be the same not-quite-compatible clones, rebadged and resold by APA. the APA 102-22C are in the mail to us now and we expect them next week. We’re hopeful that they’ll play nicer.
At the same time, we got some samples of the SK9822, another APA102C clone, directly from the manufacturer. They too turned out to use a version of the chip from the bad clones. We asked the manufacturer about the problem and after a bit of back and forth, they admitted to knowing what was going on and offered to spin us some new LEDs that trade a slightly higher power usage for being dead silent. It took a week and a half, rather than the week they promised, but those LEDs got put in the mail to us on Friday.
Next week, we hope to put the APA 102-22C LEDs and the v2 SK9822 LEDs through their paces. If neither of them works out, we’re going to start trying to find stocks of APA 102C gathering dust on distributor shelves and rope in a couple of EEs to look at other ways of quieting down the clone LEDs.
This is, of course, all incredibly frustrating and is something that should have been figured out months ago, but we’re happy that we’ve found the actual cause of the issue rather than shipped with the band-aid we’d been trying.
Next update
You should expect to hear from us again when we’re ready to ship the PVT keyboards to customers willing to take the earliest units and put them through their paces OR when our factory shuts down for the Chinese New Year festival, whichever comes first.
Thanks again for sticking with us. As much as this update is a laundry list of open issues, we believe it to be a nearly complete list of the open issues we need to resolve before we ship your keyboard to you.
<3 i+j+k